Automotive
Lightweight Construction with Particle Foam.
Fully Protected
Due to their special properties, particle foams are ideally suited for a wide range of automotive applications. For example, inserts made of particle foam have an excellent ability to absorb energy under dynamic load. Impact absorbers in the floor, in headliners and side panels, in steering column, headrests and bumpers are used primarily for the passive protection of occupants and chassis. In the case of electric vehicles, the protection of battery systems should be emphasized.
Lightly Constructed
There is no doubt that the use of particle foam is trend-setting for the construction of vehicles. Interesting features are not only the great freedom of design, but also the high structural strength at very low weight, the good resilience and the functional safety within large temperature ranges. Lightweight construction is the trend, because reducing vehicle weight saves fuel and costs, increases the range of electric vehicles and thus contributes to the reduction of CO₂ emissions. The material is already being used in innovative rear seat designs, door panels, the trunk and wheel arches, among other things.
Well insulated
The construction of electric vehicles places new demands on vehicle insulation. Particle foam can also make a contribution here: in energy management through its excellent thermal insulation values, as well as its good sound absorption capacity. In addition to the use of particle foam as the core of composite materials, the material is also increasingly used in the visible area. Attractive surfaces through laser textures and colours play an important role here.
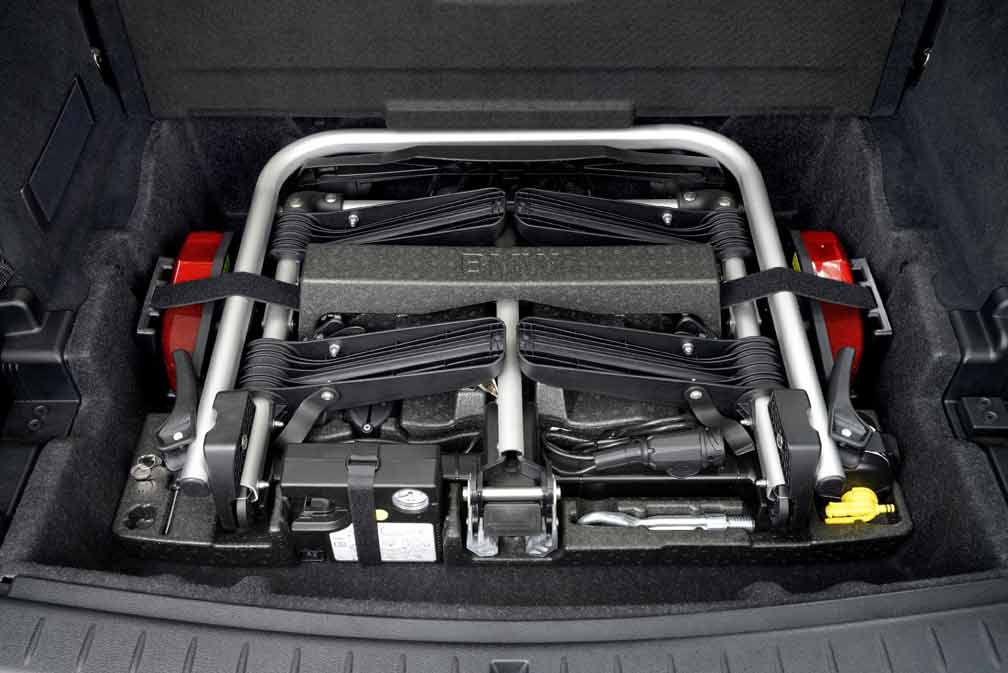
Advantages of the material
EPS (Styrofoam® | airpop®) and EPP are characterized above all by low weight and excellent energy absorption. EPP in particular can absorb a repeated impact very well. This does not cause any visible damage. These two particle foams have very good thermal insulation and optimized temperature resistance. EPP is resistant to water, most chemicals and oils and retains its structure in various applications with high loads. It also withstands temperatures from minus 25 to 130 degrees. EPS (Styrofoam® | airpop®) and EPP are 100% recyclable.
Why use particle foam in automobiles?
Particle foams have a wide range of positive properties, especially for the automotive sector, which no other material in combination can fulfil:
- high structural strength at very low weight
- great freedom of design
- very good energy absorption
- high resilience (EPP)
- fully recyclable
- good chemical resistance (EPP)
- good sound insulation/sound absorption
- excellent thermal insulation (e.g. for e-mobility)
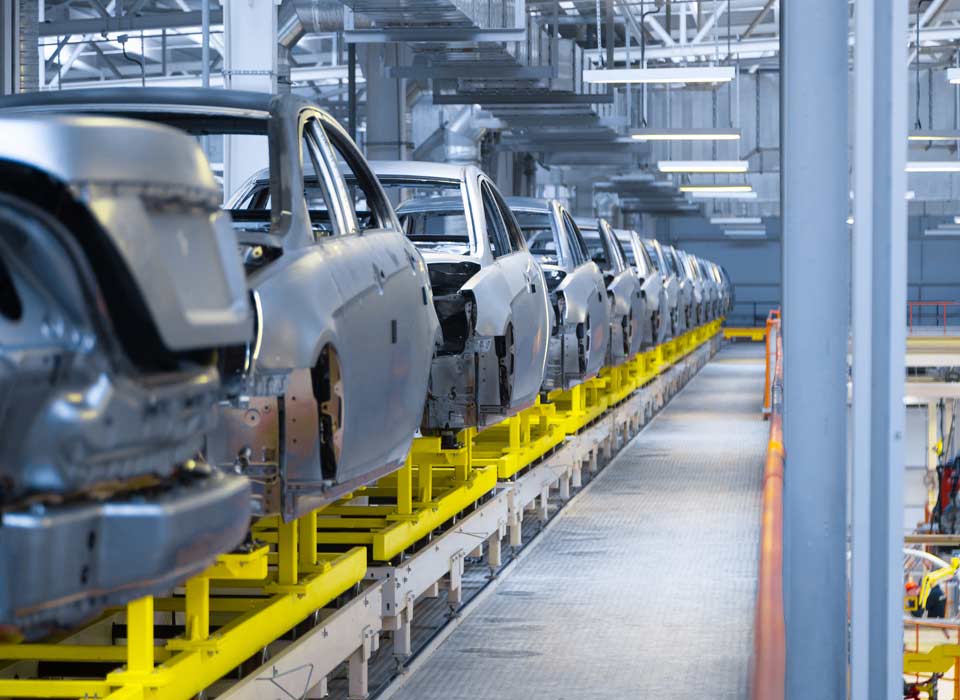
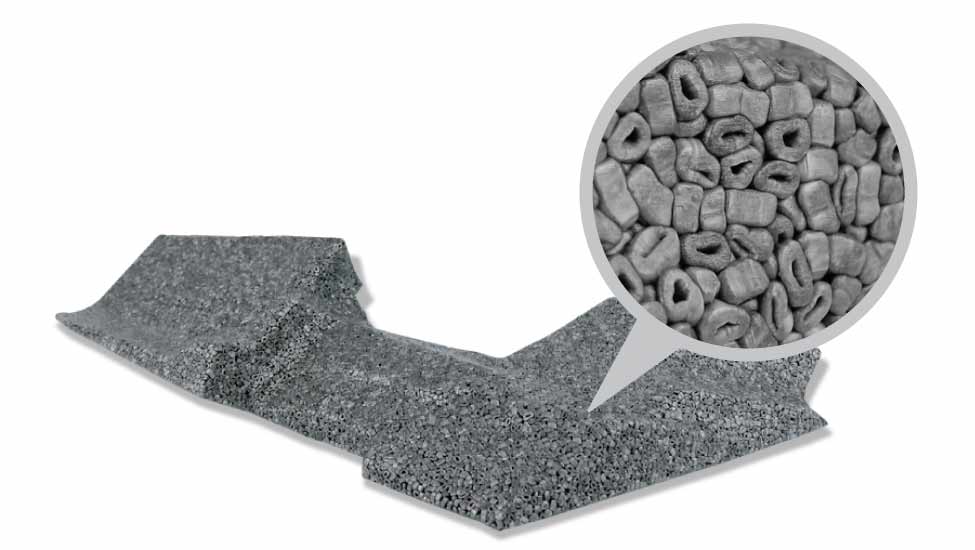
Sound insulation in automobiles
The increasing need for comfort when driving calls for innovative concepts in car body construction. Particle foam can make a significant positive contribution here. A special particle foam, p-EPP, is of particular interest for sound insulation in the automotive sector. Porous EPP has a unique cavity structure and can therefore absorb noise extremely well. Due to its porous surface, it can also be excellently foamed into e.g. carpets of the footwell.
Laser Textures
Molded parts made of particle foams are increasingly coming into view in the car body. The useful automotive parts, mainly made of the particle foam EPP, no longer disappear behind panelling or covers. In order to meet aesthetic requirements, the moulded parts are refined with attractive laser textures. Almost every imaginable pattern as well as individual customer-specific designs are possible.
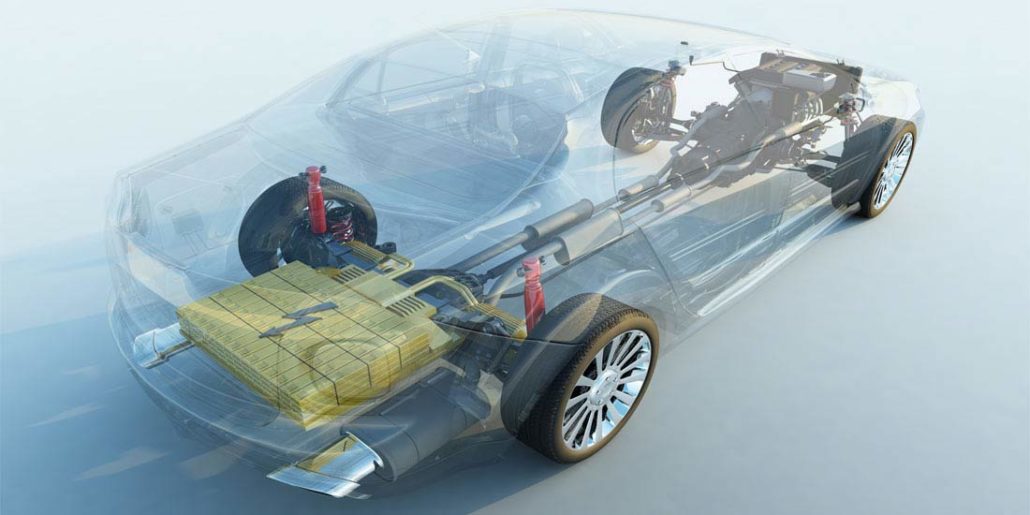
Automotive Trends
- Use as core of composite materials, e.g. body insulation for electric vehicles
- High-density crash protection elements (densities from 100 to 300 g/l) as efficient occupant/battery protection for new generations of small lightweight vehicles with low buffer zones